Eight years ago, Anglian Water developed a new hydrolysis technology to maximise biogas production from the anaerobic digestion of sewage sludge – a process that also reduced operating costs and carbon emissions. Steve Riches, Anglian’s lead for HpH technology, explains that the system is now ripe for wider adoption.
HpH technology – which stands for heating, pasteurisation and hydrolysis – separates the digestion process into two phases (hydrolysis and methanogenesis), allowing existing digesters to operate more efficiently.
The first step in the process uses hot water and steam to heat the sludge, typically this is recovered from the combined heat and power (CHP) engines that generate electricity from the biogas. The second step is pasteurisation, after which the sludge goes through a hydrolysis and acidification process, which pre-conditions it for efficient biogas conversion in the anaerobic digester.
The system has apparently raised the yield of biogas, and the renewable electricity produced from it – can you tell us more?
HpH Technology has now installed across four Anglian Water sludge treatment centres and has been operational for over 8 years. Results to date have produced an average of over 1 MWH of renewable electricity per tonne of dry solids treated from the biogas produced via its fleet of CHP engines – while producing a high-quality enhanced treated biosolids product for use in agriculture as a soil conditioner.
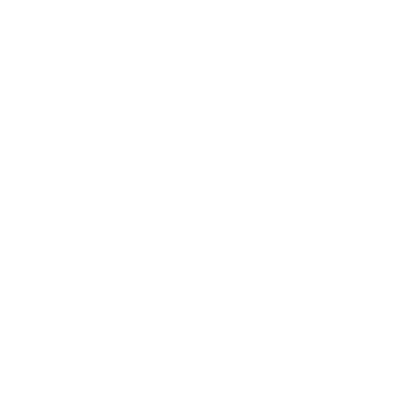
Anglian’s experience has been that gas yields have consistently been 12.5 per cent higher than other Advance Sludge Digestion technologies operated by the company and approximately 30 per cent increase when compared with conventional digestion systems, along with lower operating costs and lower capital costs delivering a lower whole-life cost of the HpH Technology compared to alternative.
What are the barriers to wider adoption outside Anglian Water?
We will continue to implement this technology at future sites in the region and have held visits by a number of other companies interested in the now proven technology and would be excited to see other companies adopt this leading technology to meet their IED , carbon and environmental challenges.
HpH is now a tried and tested technology, so barriers that may have existed before within companies to invest in unproven innovative solutions are no longer there. we expect companies with an open approach to adopt new ways of working to be open to the use of HpH Technology.
What is the pay-back period for investment in HpH?
Investment in anaerobic digestion sludge treatment technology is necessary to meet regulatory and environmental standards. Meanhwile, Anglian’s track record with HpH has shown capital costs to construct are lower, operating costs lower and income derived from the gas production is higher.
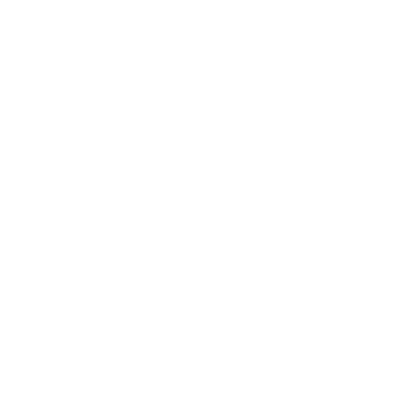
Anglian operates a range of technologies across its sites and, having taken the step to incorporate HpH, has seen significant benefits both in subsequent sludge digestion quality and standardisation.
The payback for advanced digestion technology such as HpH is influenced by a number of factors. The Anglian Water Services plants combine HpH, digestion and renewable electricity generation from combined heat and power (CHP) with the engines accredited under the now closed renewables obligations order, this gave a payback on investment of approximately three years, as a result of the additional renewable power generated and income from farm sales for the final treated product.
We would anticipate a similar strong level of payback for alternative combinations for beneficial use of biogas such as gas to grid or gas to transport.
Last year, we saw the fatal explosion at Wessex Water’s Avonmouth site. What is the safety record of the HpH plants?
Much time and consideration was given to process safety throughout the design and development of the HpH process. Additional safety features were incorporated into the design to ensure process stability and minimise the risk caused by biological process instability that is often seen in digestion processes.
The HpH process uses dynamic level control to enable close control of the biological process and also incorporates systems for foam management and over-pressure control. This significantly reduces the risk of loss of containment events compared with alternative systems available on the market.
How reliable is the process? Presumably, it relies on efficient pumping, but are stoppages and pump breakdowns a problem?
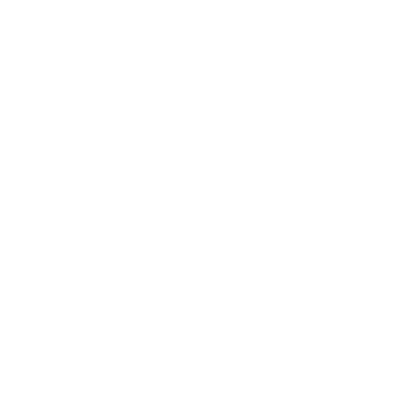
The system has proven to be reliable over the eight years of operation, our teams of bioresources technicians closely monitor plant performance parameters; this includes sampling and analysis of feed and outlet sludge to optimise process performance but also all of the key plant and equipment such as pumps and heat exchangers.
The plant is designed such that the critical pumps for the forward flow and recirculation for heating and cooling are configured as ‘duty’ and ‘standby’, thus providing a high level of reliability.
Is Anglian exploring any alternative technologies that could further improve biogas yields?
Anglian Water has explored alternative and complementary technologies to further increase gas yield and with our ‘always exploring’ principles we continue to do so, regularly engaging with suppliers and academia.
What is the next step for HpH Technology?
Anglian Water will continue to promote the technology with the intention that others will recognise the benefits and adopt the technology at future sludge treatment centres in their regions.