You’ve reached your limit!
To continue enjoying Utility Week Innovate, brought to you in association with Utility Week Live or gain unlimited Utility Week site access choose the option that applies to you below:
Register to access Utility Week Innovate
- Get the latest insight on frontline business challenges
- Receive specialist sector newsletters to keep you informed
- Access our Utility Week Innovate content for free
- Join us in bringing collaborative innovation to life at Utility Week Live
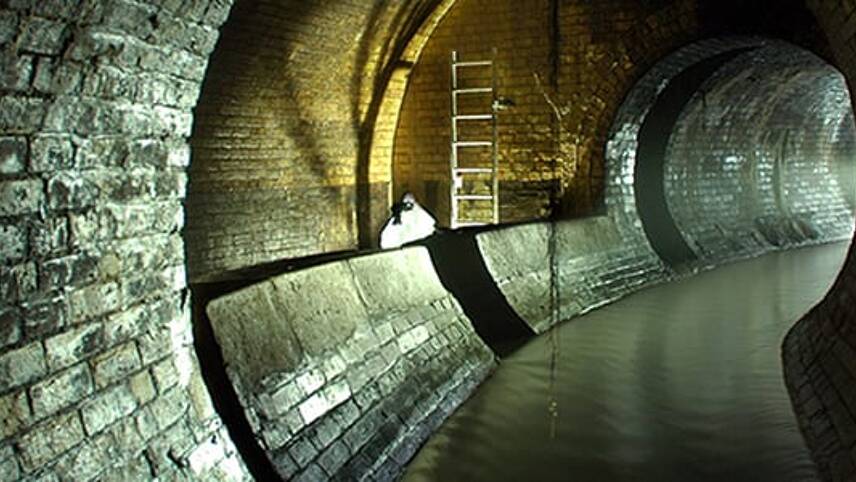
Drains and sewers are a vital part of any new housing development, and developers need to make early decisions on their design and construction, writes Andy Cullum
The newly-elected Conservative Government has pledged to create 275,000 affordable homes by 2020. With this in mind, the volume of applications for Section 104 agreements looks set to increase exponentially. To avoid delays and extra cost to their projects, developers will need to consider drainage design and make key decisions – including the choice of materials – as early as possible.
What is a Section 104 agreement?
A Section 104 agreement (under the Water Industry Act 1991) is an agreement between a developer and sewerage undertaker for the adoption of sewers serving a development. There are strict regulations in place for obtaining an agreement which can be a minefield for developers. The process is often on the critical path of a project and the decisions involved can have huge cost implications. In Wales, the Mandatory Build Standards dictate that a Section 104 agreement needs to be in place before a development can progress. With this legislation likely to be implemented in England, it’s vital that all stakeholders in residential build projects understand the process.
What is the process for getting an agreement?
The route to reaching a Section 104 agreement begins with an initial flood risk assessment, and takes into account the drainage requirements for the entire site to ensure that local sewerage and surface water drainage systems are considered and not overwhelmed.
The appointed Consultant Engineer will initiate a design based on the management of stormwater against a chosen storm design return period and an agreed discharge limit. This is typically done for both a ‘1 in 30’ year and ‘1 in 100’ year storm event, plus allowance for climate change, with the former being most frequently adopted by the relevant sewerage undertaker and the latter usually managed privately.
Along with Sewers for Adoption guidelines, the sewerage undertaker and local authorities may also have specific requirements that need to be considered, including (but not limited to) the system’s design requirements and products approved for use.
How can manufacturers help in the process?
As well as providing approved products, reputable manufacturers can assist the Consultant Engineer with various design solutions and help to provide assistance with a ‘fully engineered design’ if engaged with as early as possible in the process. This can help to overcome problematic schemes, allowing the Section 104 application and Drainage Strategy to be accepted and approved with the most appropriate material first time, reducing costly resubmissions and delays on site.
Some manufacturers also offer supporting detailed drawings and structural calculations to BS EN 1295-1 (1997): Structural Design of Buried Pipes under various conditions of loading. These designs consider the ground conditions on site to ensure that the specified solution is neither over or under engineered. Storage volume calculations can also be provided to help evaluate the SuDS footprint, maximising the space available for development amenity.
How long does the approval process take?
The Consultant Engineer will carry out hydraulic and structural calculations and submit a design proposal to the relevant Developer Services department within the approving sewerage undertaker for approval.
From here, the approval process can take approximately six weeks, sometimes longer, once the design has been completed and issued. It is key to select the right material type before submission.
What are the considerations in drainage system choice?
When designing, commissioning and maintaining pipe systems for adoption in Section 104 agreements, developers and their chosen designers have a wealth of product and material options open to them, and have a number of considerations to account for.
The most obvious is perhaps in the system’s overall design, including the length of pipe runs and whether there are any elements necessary to ensure the flow of water through the system is controlled to an adequate rate for the sewer network.
The choice of pipe material is key for design, commissioning and maintenance teams. While traditional materials such as concrete have been used in the past for large diameter sewers, an ever growing number of developments feature tried and tested engineered plastic systems that can be optimised to site conditions in order to unlock a host of cost and time savings.
What are the advantages of plastic pipes for these applications?
Designers can confidently specify thermoplastic structured wall pipe systems, as all of the UK’s main water companies have approved the use of plastic pipework, chambers and fittings in diameters from 150mm through to 3000mm.
By their nature, these products are able to be easily designed into varying configurations to meet the needs of the site exactly. Manufactured under quality controlled factory conditions, plastic can be utilised to produce fully engineered modular pre-fabricated drainage systems and chambers.
This ability to produce pre-fabricated items to meet the needs of the site is a major benefit in making maximum use of the space available. Pipes manufactured in this way can be designed in a range of profiles and stiffnesses; the latter being a vital consideration if systems are to be installed beneath roads and paved structures in line with Section 38 of the Highways Act (1980).
Utilising plastic products also offers a host of benefits during installation, commissioning and maintenance. It stands to reason that modular systems delivered to site ready for installation would be favoured by contractors, but being lighter in weight and easier to handle than traditional alternatives means that plastic products offer a host of time saving and health and safety benefits.
As well as being durable and robust, thermoplastic structured wall pipe systems can be integrally socketed for improved pipe alignment for easier installation and smoother hydraulic performance, vital for a design life of over 100 years with low maintenance. A wide variety of jointing options are available, from electro-fusion welding for high specification projects to ring seals for simpler installations.
The versatility of plastic pipe systems means that a range of manholes that can be benched and channelled in accordance with Sewers for Adoption specification are also available, ensuring water flows through the system with reduced blockages to reduce maintenance requirements.
What can be done to ensure the process goes smoothly?
Forward planning is the key to success. Good planning and design begins with an understanding of both the site considerations and constraints. Drainage material type should be considered at the start of the project, preferably at the master planning stage.
Although experienced Consultant Engineers are more than capable of producing suitable system designs of their own accord, the best outcomes are often secured through proactive pre-Section 104 application discussions between developers, local authorities and water management specialists.
Having a slick design and submission process often means that sewers can be adopted more easily and the bond released back to the developer – often resulting in a quicker, more profitable build programme.
In order to successfully have water management strategies approved and a Section 104 agreement in place, it’s essential to assess the needs of the individual site in order to provide the optimal solution.
Please login or Register to leave a comment.